What are the principles of LISUN glow wire tester?
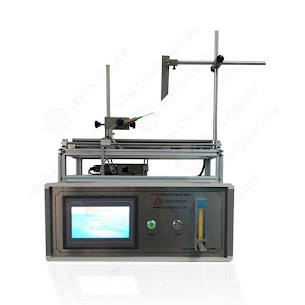
The LISUN glow wire tester is a device that simulates real-life situations in which a product might catch fire in order to determine how likely it is that an electrical or electronic piece of equipment would catch fire in the event of an accident. The LISUN glow wire tester operates according to the following guiding principles: Measurement of temperature: This glow wire tester makes use of a thermocouple, which is brought into direct contact with the wire in order to get an accurate reading of the wire's temperature. Ignition source: the wire is heated by an electrical current, and once it reaches a particular temperature, it will ignite, mimicking a fire danger. Once it reaches this temperature, the wire will ignite. Preparing the Specimen: The specimen for testing is prepared by securing it to the testing apparatus in a manner that replicates the circumstances that would be present in actual use. Test technique: The testing procedure consists of heating the wire to a certain